Properties, Processing Methods of Wool and Rayon
Wool
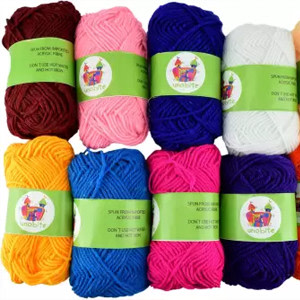
Wool is an ancient fibre created by nature that has been used by man for centuries for its warmth and durability. Different kinds of animals have been used for textile fibres. Wool is a hair fibre made up of fibrous protein called Keratin and comes from fleece of sheep and also some other animals such as Angora, Cashmore, Camel, Alpaca. Despite all the technological advancement in alternative synthetic materials, wool remains a unique, and almost miraculous fibre with its ability to absorb a high level of moisture while simultaneously providing protection from rain showers.
Let us explore the various steps involved in the processing of wool . . .
Let us explore the various steps involved in the processing of wool . . .
Wool Processing
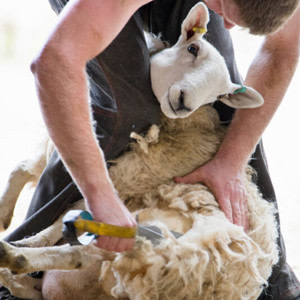
Shearing
Sheeps are sheared to remove the fleece in the spring season. Expert shearers move from place to place removing fleece. A section is kept seperate for fleece from sides of the sheep. This is done because the fleece from undersection and legs tend to be inferior in quality to that of the sides because it contains more vegetable matters and is tangled with thorn. Fleece is sheared from sheep at 8 months of age or younger. Younger is called lamb's wool because it is the first growth of hair with tapered ends it tends to be softer and finer. Wool removed from animals that have been slotted for meat is reffered as pulled wool. Pulled wool is inferior in quality to fleece or clipped wool because it is less elastic.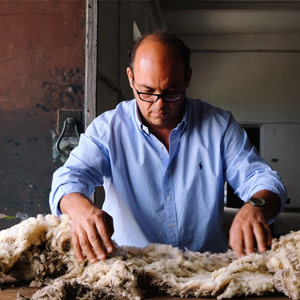
Grading
Grading of wool is done at the time of shearing. In grading, the fleece is judged for its overall fibre fineness and length. An alternative to grading is found in sorting in which the fleece is divided into section of different quality. The best fibre comes from the sides and shoulders, the poorest from the lower legs.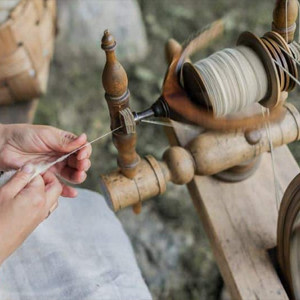
Preparation of Spinning
The first step taken to prepare the fleece for use is scouring, which removes oil, greece and other impurities from the fleece. The fleece is washed a number of times in a warm soapy solution, A fleece about 8 pounds will be reduced by scouring to about 3 to 4 pounds. Much of weight loss results from te removal of a natural oil covered by it. After that all the fibres are carded and then spinning is given.Properties of Wool
1. Color
Wool fibres vary in nature. Color being white to cream to light yellow, brown and black. Wool may bedyed easily however it is difficult to keep it white. Bleaching is not given to wool because it is harmfulfor fibres or that itself may cause for yellowing.2. Shape
The length of the fibre depends on the breed of the sheep from which it comes. The length ranges from 1 - 15 inches or more. The outer layer consists of small overlapping scales. The scales on the surfaceof fibre overlap like the tiles on a roof.3. Lustre
The lustre of the wool is low because of the scaly rough surface. Lustre varies amoung different breedsof sheep, different section of fleece.Environmental Properties of Wool
Fabric should be put away only after they are completely dry. One of the major problems in the case ofwool is its possibility of damage from insects. Care in the storage of wool is required. Mildew wil not form on wool unless the fabric has been stored in a damped condition for an extended period of time.Mohair
Mohair is a silky cloth made from the hair of Angora goats.Rayon
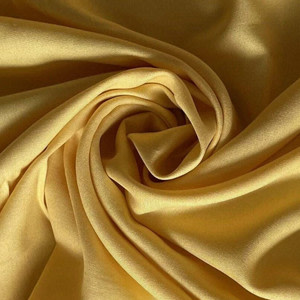
Rayon is the first manmade fibre. It has been called "The laboratory's first gift to the loom". Rayon is considered to be one of the most versatile and economical manmade fibres available. It is a regenerated fibre derived from wood pulp, cotton linters or other vegetables matters. Because of its lustre and softhand feel, it resembles silk thus it is also known as artificial silk or art silk.
Manufacturing Process of Rayon
1. | Cellulose | - | Production begans with processed wood pulp. |
2. | Steeping | - | The cellulose is dissolved in canstic soda (Sodium hydroxide - NaOH). |
3. | Pressing | - | The solution is then pressed between rollers to remove excess liquid. |
4. | Shredding | - | The pressed sheets are crumbled or shredded to produce what is known as white crumb. |
5. | Aging / Ageing | - | The white crumb is allowed to stand in contact with oxygen in the air. |
6. | Xanthation | - | The aged white crumb is mixed with carbon disuphide in a process known as Xanthation. The aged Alkali cellulose crumbs are placed in vats and are allowed to react with carbon disulphide under controlled temperature to from cellulose Xanthate. Xanthation changes the chemical makeup of the cellulose mixture and the resulting product is called yellow crumb. |
7. | Dissolving | - | The yellow crumb is dissolved in caustic solution to form viscose. |
8. | Ripening | - | The viscose is allowed to stand for a period of time to ripen. |
9. | Filtering | - | After ripening the viscose is filterd to remove any undissolved materials that might disrupt the spinning process or cause defects in the rayon filament. |
10. | Degrassing | - | Bubbles of air are removed from the viscose is a degrassing process. |
11. | Spinning | - | The viscose solution is extreded through a spinneret (It resembles a shower head with many holes). As the viscose exits the spinneret it lands in an acid bath (Sulfuric acid, sodium sulphate and zinc) resulting in formation of rayon filament. |
12. | Drawing | - | Rayon filaments are stretched known as drawing, to straighten the fibres. |
13. | Washing | - | The fibre are then washed to remove any chemicals(impurities). |
14. | Cutting | - | If filament fibres are desired the process ends here. The filaments are cut down when producing staples fibres. |
Properties of Rayon
1. Color and Lustre
The rayon fibres are normally white in color. Their lustre can be modified by adding titanium dioxidedelusterting agent to the solution before the fibres are extruded.2. Shape
Manmade fibres can be manufactored in any length and diameters. In cross section the viscose rayonfibres appears as irregular circles with srerated (having a toothed edge) edges.3. Strength
Strength of viscose rayon is low when compared with cotton or linen.Rayon Fibre Characterstics
- Highly absorbent
- Soft and comfortable
- Easy to dye
- Drapes well
Please leave your comments, we do love it!
Most Viewed Articles
Hey, we have amazing content on the latest Fashion, Trends, Style & Creative Arts, and now it's absolutely FREE for you.All you have to do, is just...We always respect your privacy!
Login / Sign-up